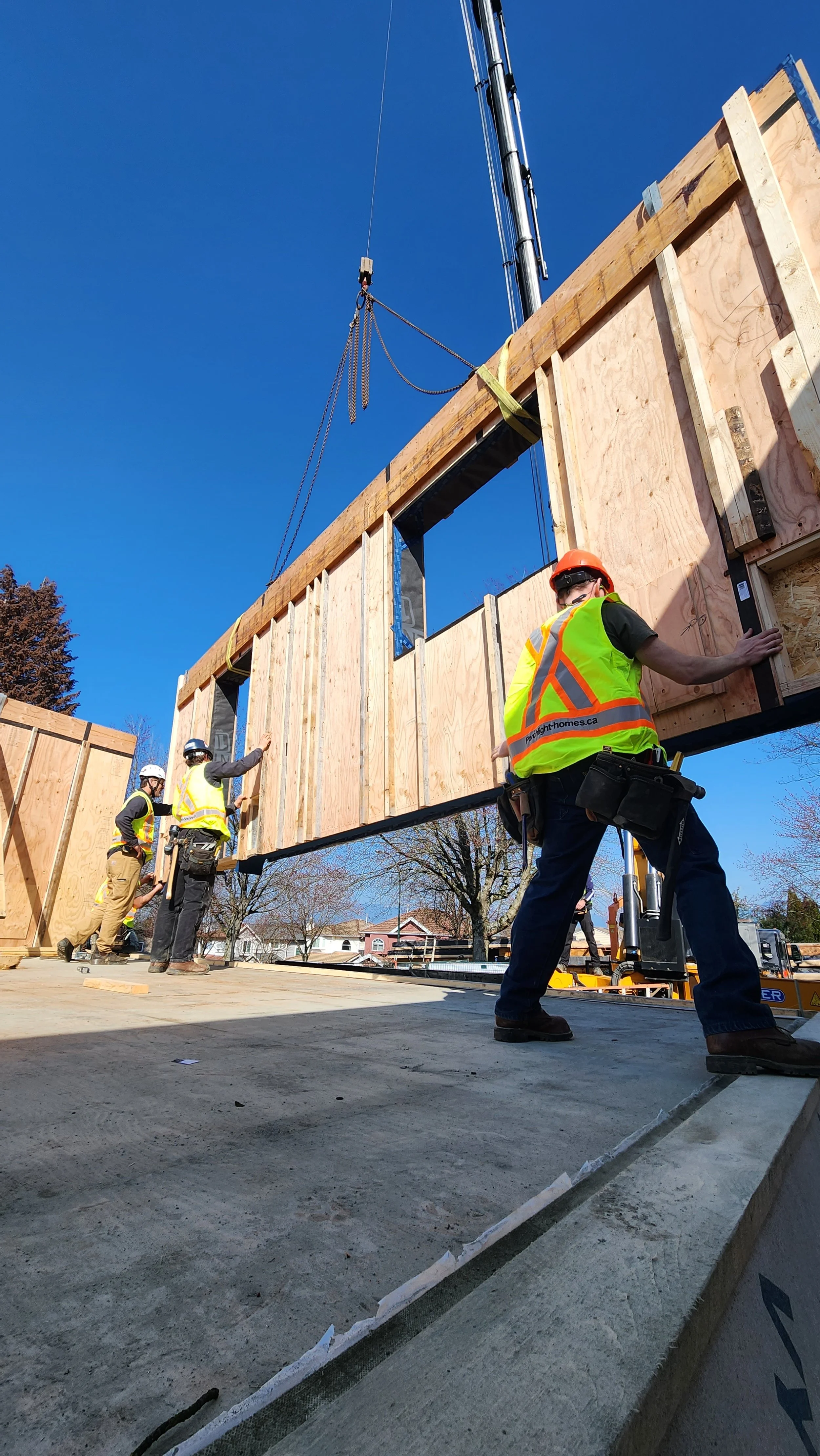
Frequently Asked Questions
Find answers to common questions and get the help you need with our comprehensive FAQ.
Frequently asked questions
-
BOSS stands for Building Offsite Sustainable Systems. It is an open source system designed to help reduce the risk associated with offsite closed panels by providing a flexible and sustainable housing solution that incorporates passive house principles, low embodied carbon materials, and 100% electric and renewable energy sources.
-
BOSS is an offsite, wood-based construction solution that is designed to meet the needs of diverse communities throughout British Columbia. The system uses closed panels that are pre-fabricated in a controlled factory environment, which helps to ensure quality and consistency. These panels can be customized to meet specific design requirements and can be quickly assembled on-site.
-
BOSS offers a number of benefits over traditional construction methods, including reduced construction time and cost, improved energy efficiency, and reduced environmental impact. The system is also highly customizable and can be adapted to meet the needs of different communities and housing types.
-
While BOSS is highly flexible and can be customized to meet a variety of building requirements, it may not be suitable for all types of buildings. It is important to consult with a qualified engineer or architect to determine whether BOSS is appropriate for your specific project.
-
Yes, BOSS is certified for use in British Columbia and meets all relevant building codes and regulations
-
Yes, BOSS homes are highly customizable and can be designed to meet a variety of design requirements and specifications.
-
Construction times will vary depending on the specific project requirements, but BOSS homes are generally faster to construct than traditional homes.
-
BOSS homes can be more cost-effective than traditional construction methods, particularly when considering long-term energy savings and reduced maintenance costs.
-
Yes, BOSS can be used for a variety of construction projects, including commercial and multi-family residential buildings.
-
Yes, BOSS incorporates low embodied carbon materials and 100% electric and renewable energy sources, making it a highly sustainable and environmentally friendly option for housing construction.
-
BOSS (Building Offsite Sustainable Systems) is an open-source prefabrication system that was developed by a team of experts and funded by Clean BC. As an open-source system, BOSS is not owned by any one person or organization, but is available to the public for use and modification. The development of BOSS was a collaborative effort involving architects, engineers, builders, and other industry experts who worked together to create a flexible and sustainable housing system that meets the needs of diverse communities throughout British Columbia. The goal of BOSS is to reduce the risk associated with offsite closed panels and to promote sustainable and energy-efficient construction practices. While BOSS is not owned by any one person or organization, there are groups and individuals who are involved in its ongoing development and promotion. These groups and individuals may include industry associations, builders, architects, engineers, and others who are committed to advancing the use of prefabricated construction methods and sustainable building practices. Overall, BOSS is a collaborative and open-source system that is available to anyone who is interested in using it to build sustainable and energy-efficient buildings.
-
BOSS buildings typically involve the work of multiple professionals, including envelope and structural engineers. These professionals provide design specifications and schedules to ensure that the building meets all relevant building codes and regulations. The envelope engineer is responsible for designing and specifying the building's exterior envelope, including the walls, windows, doors, and roofing system. They work to ensure that the building is protected from the elements and that the envelope system is energy efficient and meets all relevant codes and regulations. The structural engineer is responsible for designing and specifying the building's structural system, including the framing, foundation, and load-bearing elements. They work to ensure that the building is structurally sound and meets all relevant codes and regulations. Both the envelope and structural engineers provide design specifications and schedules that are critical to the construction of BOSS buildings. These specifications and schedules outline the materials, construction methods, and quality control measures that are necessary to ensure that the building meets all relevant codes and regulations. During the construction process, inspections are typically carried out by local building inspectors to ensure that the building is being constructed according to the approved plans and meets all relevant building codes and regulations, including those related to the envelope and structural systems. The inspections may also involve reviews of the design specifications and schedules provided by the professionals involved in the project. By working with qualified professionals like envelope and structural engineers and following their design specifications and schedules, BOSS buildings can be designed and constructed to meet all relevant building codes and regulations, ensuring that they are safe, durable, and energy efficient.
-
To use BOSS on your next project, you will need to follow a few key steps: Review documentation: The first step is to review the BOSS documentation, which includes design guidelines, construction specifications and other information related to the use of the BOSS prefabrication system. This documentation is available for download from the resources page. Engage a BOSS Consultant: To ensure quality assurance and quality control, it is recommended to engage an experienced BOSS consultant at the start of the project. By engaging an experienced consultant who is familiar with the system, you can ensure that the builder is following the design specifications and that the project is being constructed to the highest standards of quality and efficiency. The experienced consultant can also provide guidance and support throughout the project, helping to ensure that any issues or challenges are addressed in a timely and effective manner. Engage a design professional: The BOSS system requires the involvement of a qualified design professional, such as an architect or engineer, to ensure that the building meets all relevant building codes and regulations. Customize the design: The BOSS system is designed to be flexible and adaptable to a wide range of building types and configurations. Working with the design professional, you can customize the design to meet your specific project requirements. Fabricate the panels: Once the design is finalized, the panels are fabricated in a controlled factory environment, using the BOSS prefabrication system. This ensures that the panels are high quality, consistant, and that they meet all relevant building codes and regulations. Transport and assemble the panels: Once the panels are fabricated, they are transported to the building site and assembled according to the design specifications. This process is typically faster and more efficient than traditional construction methods, and can help to reduce construction time and costs. Overall, using the BOSS prefabrication system on your next project requires careful planning and coordination with qualified professionals. By following the design guidelines and working with a BOSS Consultant and design professional, you can ensure that your project is built to the highest standards of quality, sustainability, and energy efficiency
-
The process of engaging an experienced BOSS consultant typically involves the following steps: Initial consultation: The first step is to schedule an initial consultation with the BOSS consultant to discuss your project requirements and goals. During this consultation, the consultant will review your project plans and provide feedback on how the BOSS prefabrication system can be integrated into your project. Design review: Once the consultant has a clear understanding of your project requirements, they will review your project design to ensure that it meets all relevant building codes and regulations, as well as the BOSS design guidelines and specifications. Builder selection: The consultant will help you select a BOSS-approved builder who has been trained in the use of the BOSS prefabrication system. The builder will be responsible for fabricating and assembling the BOSS panels on-site. Quality assurance and quality control: Throughout the project, the consultant will provide ongoing support and guidance to ensure that the project is being constructed according to the design specifications and BOSS standards. This includes conducting regular quality assurance and quality control checks to ensure that the BOSS panels are being fabricated and assembled to the highest standards of quality and efficiency. Project completion: Once the BOSS panels have been fabricated and assembled on-site, the consultant will conduct a final inspection to ensure that the building meets all relevant building codes and regulations, as well as BOSS standards. At this stage, any necessary adjustments or corrections will be made to ensure that the building is ready for occupancy. Overall, the process of engaging an experienced BOSS consultant is designed to ensure that your project is built to the highest standards of quality, sustainability, and energy efficiency. By working with an experienced consultant and a BOSS-approved builder, you can ensure that your project is completed on time and on budget, with minimal disruption to the surrounding community.
-
BOSS provides a range of prefabricated building components that are designed to meet the highest standards of sustainability, energy efficiency, and durability. Currently, the system includes the following components: - Structural building components for walls, both exterior and interior - Floor system cassette - Gable walls and roofs, depending on the type of architecture The panels are constructed using a combination of high-quality materials, including: - 1 ½” reclaimed lumber for the interior mechanical cavity - ½” plywood sheathing, taped for air and moisture barrier - Wide format structural stud options, such as dimensional 2x__ or thermally broken studs - Filled with dense pack cellulose or other insulation options - LSL bottom and top plate, 1 ¾” x 9 ½” - Interchangeable exterior sheathing layer, such as wood fiber board, Rockwool Comfo Board 80, DensGlass (fire rating), or ½” plywood (use and occupancy load reviewed) - Water-resistant barrier (WRB), specified by a qualified professional - ½" x 1 ¾" wide pressure-treated plywood strips These building components are designed to be highly customizable and adaptable to a wide range of building designs and construction methods. By using BOSS components, builders can streamline the construction process, reduce waste, and achieve higher levels of energy efficiency and sustainability in their buildings.
-
BOSS is designed to meet or exceed the requirements of the BC Energy Step Code, including the highest level of Step 5 (Net Zero Energy Ready). The system incorporates passive house principles, low embodied carbon materials, and 100% electric and renewable energy sources to help builders meet the highest standards of energy efficiency and sustainability. By using BOSS components, builders can achieve high levels of insulation, airtightness, and thermal bridging reduction, which are key requirements for achieving net zero energy and other high-performance building standards.
-
BOSS is a light wood frame construction system, and currently, it can be used to build up to 6 stories in height. This limit is based on the current building code requirements and engineering standards for light wood frame construction. However, BOSS is a flexible and customizable system that can be adapted to meet the needs of a wide range of building designs and construction methods. Future updates to building codes and engineering standards may allow for even taller buildings to be constructed using BOSS components
-
Mechanical systems can be easily integrated into the BOSS system, allowing for efficient and effective distribution of electrical, plumbing, and ventilation systems throughout the building. The system takes an integrated design approach, working closely with consultants and trades to ensure that mechanicals are fully integrated into the overall design and construction process. For example, the BOSS wall panels include a mechanical cavity on the interior side, allowing for easy installation of electrical wiring, outlets, and light controls in compliance with building codes. Additionally, the floor cassettes and interior walls can be designed and built to accommodate plumbing and ventilation systems, ensuring that mechanical systems are efficiently distributed throughout the building. With careful planning and coordination, mechanical systems can be seamlessly integrated into the BOSS system, resulting in a highly functional and sustainable building.
-
BOSS currently has a single family project in Vancouver underway with more in the planning stages. BOSS is a new and emerging system that has not yet been widely adopted for large-scale projects. The system has undergone extensive testing and validation, and it has been used in a number of pilot projects and prototypes. As interest in offsite construction and sustainable building practices continues to grow, it is likely that BOSS will become more widely adopted in the coming years.
-
There are many benefits to using BOSS and offsite construction techniques for building projects, including: 1. Speed and efficiency: Offsite construction methods, such as those used by BOSS, can significantly reduce construction timelines by allowing for simultaneous site preparation and panel fabrication. This can lead to faster project completion times and reduced construction costs. 2. Quality control: By fabricating building components in a controlled factory environment, BOSS can ensure consistent quality and precision in each panel or module. This can result in higher quality buildings with fewer defects and issues. 3. Sustainability: BOSS is designed to be a sustainable building system, with a focus on using low embodied carbon materials, passive house principles, and 100% electric and renewable energy sources. By reducing the carbon footprint of building construction, BOSS can help to mitigate climate change and reduce environmental impact. 4. Cost savings: Offsite construction can help to reduce labor costs by allowing for more efficient use of skilled workers and reducing on-site labor requirements. This can lead to overall cost savings for the project. 5. Flexibility: BOSS is a flexible system that can be adapted to meet the needs of a wide range of building designs and construction methods. This allows for a greater degree of design freedom and customization, while still leveraging the benefits of offsite construction. BOSS and offsite construction can provide a range of benefits for building projects, from improved speed and efficiency to sustainability and cost savings.
-
The engineering and architectural inspection process for BOSS projects is typically handled in several stages. First, the project design and engineering plans are reviewed and approved by qualified professionals, including structural engineers, envelope consultants, and mechanical engineers as needed. These professionals work together to ensure that the building design and components meet or exceed all relevant codes and standards. Once the project is underway, inspections are typically carried out at various stages of construction, including during the fabrication and assembly of the prefabricated components, as well as during installation and finishing stages on site. These inspections are typically carried out by qualified inspectors or engineers, who will review the work and ensure that it meets all necessary codes and standards. The inspection process is an important part of ensuring the quality and safety of BOSS projects, and BOSS works closely with qualified professionals to ensure that all necessary inspections are carried out and all relevant codes and standards are met.
-
BOSS uses a CAD CAM (computer-aided design/computer-aided manufacturing) process to design and fabricate its building components. This process involves using advanced software tools to create detailed 3D models of the components, which are then translated into instructions for computer-controlled machines that cut and shape the materials to precise specifications. The CAD CAM process enables BOSS to achieve a high level of precision and consistency in the fabrication of its building components, which helps to ensure that each component fits perfectly into place during the assembly process. It also allows for efficient and streamlined production, which can help to reduce costs and increase productivity. The CAD CAM process is an integral part of BOSS's prefabrication methodology, and is key to the success of the system. By leveraging advanced technology and best practices in manufacturing, BOSS is able to deliver high-quality, sustainable, and cost-effective building solutions that meet the needs of clients and communities throughout British Columbia.
-
If you're referring to offsite constructed closed panels used for building construction, these panels are typically regulated by the building code and require approval from the local building department. The approval process typically involves a review of the panel design and materials used to ensure compliance with the building code and any applicable local regulations. The CSA is also involved in the certification of some offsite constructed building components, including wall panels. However, the specific requirements for certification may vary depending on the intended use and location of the panels. If you're planning to use offsite constructed closed panels in a building project in British Columbia, it's important to work with a qualified engineer or architect who can help ensure that the panels meet all the necessary requirements and regulations. They can help ensure that the panels are properly designed and constructed to provide safe and reliable building components.